
How are Stainless Pipe Fittings Made?
In the world of industrial manufacturing, the creation of stainless steel butt-weld pipe fittings is a process that combines technological precision with meticulous finishing techniques. Widely appreciated for their durability and resistance to corrosion, these fittings are integral components in various applications, from plumbing and gas fitting to the automotive industry. Let's delve into the fascinating journey of how stainless steel butt-weld pipe fittings are made, from raw material to the finished product.
We are often asked if our pipe size elbows, commonly referred to in the automotive fabrication industry as "Weld Els," are cast. Despite their appearance, the Ace Race Parts brand of stainless steel pipe fittings and straight lengths of pipe are not actually cast fittings. In fact, these fittings are crafted using a "hot forming" technique.
UNDERSTANDING THE MATERIAL: 304 and 321 STAINLESS STEEL
304 stainless steel, known for its excellent corrosion resistance and value, is the most common stainless steel used in aftermarket exhaust systems and turbo manifolds. Comprising a combination of iron, chromium (at least 18%), and nickel (up to 8%), this alloy strikes the perfect balance between strength and workability.
321 stainless steel is another popular choice for automotive fabricators. While similar to 304 stainless steel in many respects, 321 stainless steel contains titanium, which stabilizes the alloy against chromium carbide precipitation. This stabilization makes 321 stainless steel more suitable for high-temperature applications, such as those found in exhaust systems, turbo manifolds, and aerospace components.
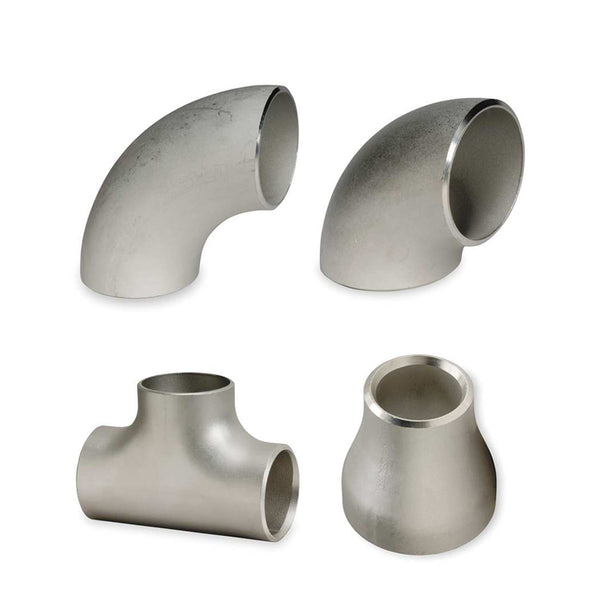
The Manufacturing Process
Forming the Shape:
The process of creating 304 and 321 stainless steel butt-weld pipe fittings begins with careful consideration of the desired shape and dimensions. Unlike casting, where molten metal is poured into a mold, these fittings are formed through a method known as hot forming.
Firstly, raw stainless steel material is sourced, typically in the form of sheets or bars. These raw materials undergo heating in specialized furnaces to extremely high temperatures, reaching well above the metal's recrystallization point. This heat treatment softens the stainless steel, making it malleable and ready for shaping.
Depending on the desired outcome, there are two primary methods for forming these fittings: seamless and welded.
For seamless fittings, the heated stainless steel is extruded through a die to form a seamless tube. This extrusion process ensures a uniform structure and consistent thickness throughout the length of the tube. Once the tube reaches the desired length, it is cut using precision machinery.
In the case of welded fittings, the heated stainless steel is manipulated into shape using rolling and bending techniques. Sheets of stainless steel are rolled into cylindrical shapes and then welded along the seam to create a strong, continuous structure. These welded seams undergo additional treatment to ensure their integrity and strength.
Cooling and Finishing:
After the initial shaping process, the newly formed fittings are cooled gradually to room temperature. This cooling period is carefully controlled to prevent distortion or stress within the metal, ensuring the final product maintains its structural integrity.
Once cooled, the fittings undergo a series of finishing processes to refine their surface quality and dimensional accuracy. These finishing techniques may include machining, grinding, and polishing, depending on the specific requirements of the application. Each fitting is meticulously inspected to ensure it meets the precise specifications outlined by industry standards.
The Art of "Pickling"
A pivotal part of the finishing process is "pickling." This involves immersing the fittings in a chemical bath designed to remove any surface impurities, stains, rust, or scale. The pickling process not only cleans the metal but also imparts a matte finish that closely resembles the surface of cast products. However, it's essential to understand that this resemblance is purely aesthetic—the properties and performance of the fittings are rooted in their robust manufacturing process.
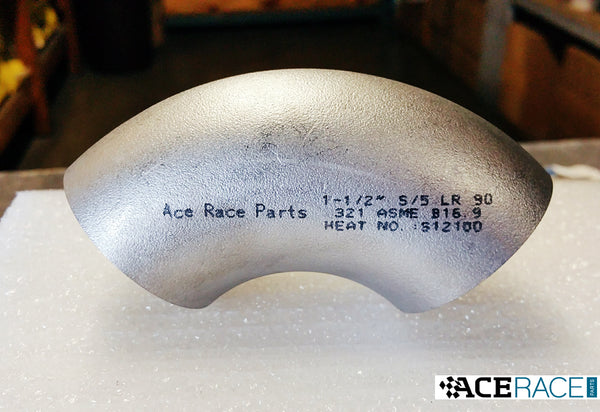
The Illusion of Casting
It's fascinating how the finishing touches can influence our perception of how a product is made. While stainless steel butt-weld pipe fittings might appear to be cast due to their smooth and uniform finish, it's the combination of high-temperature forming and precise finishing that truly defines their quality. This distinction is crucial for industry professionals who rely on the specific characteristics of these fittings for their projects.
Conclusion
The manufacturing of 304 and 321 stainless steel butt-weld pipe fittings is a testament to the sophistication and precision of modern metallurgy. By understanding the steps involved in their production, we gain a deeper appreciation for the engineering and craftsmanship that ensure these fittings meet the highest standards of quality and performance. Whether it's the heat of forming or the meticulousness of pickling, each stage of the process plays a pivotal role in delivering a product that appears deceptively simple yet is complex in its creation.
Leave a comment